Ultrasonic leak Audit
Ultrasonic leak Audit
Ultrasonic leak Audit
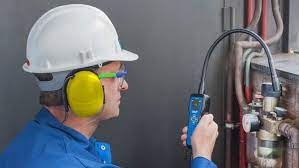
Compressed air installation of more than 5 years old has an average 25% of air leakage. Air leaks are a big waste of energy, but easy to ignore. In a typical industrial plant, compressed air accounts for up to 35% of the total electricity bill. Any leakage generated from compressed air will cause a huge amount on your bill.
Why does an Air Leakage occur?
Air leakages are one of the operating concerns of using compressed air systems. But timely leak tests and scheduled maintenance can help avoid compressed air leak and ensure the longevity of your compressor. Here are some reasons why air leakages happen.
Rich in moisture content, untreated or semi-treated air may enter the air network and begin damaging the internal parts of the pipes. This reason is by far the most common reason for air leaks.
Therefore, addressing leaks is critical for reducing energy costs and maintaining sustainable production in your unit.
Wrong material selection for piping your compressed air system is also a reason that leads to erosion of the pipes. For example, bare CS pipes can result in surface corrosion.
Undersized pipes and loose joints can also generate a high velocity, leading to pipe corrosion and subsequent air leakage.
Is your air compressor leaking air? Wonder how to detect them? Read our blog telling you the signs to look for when detecting air leakage in your compressor air system.
What is an Air Leak Test and why conduct it?
Conducting an air leak test at the right time can prevent the leakage issues from affecting the final user points. To put it simply, an air leaking test is an evaluative method to scan for leakage issues and analyze pressure in your air compressor. Following are the benefits of performing an air leak test:
Leak standards are quantified
Product efficiency is optimized
Time and work saving with automation
Operational and energy costs are reduced
Measurement data ensure product improvement
Leak standards are quantified
Product efficiency is optimized
Time and work saving with automation
Operational and energy costs are reduced
Measurement data ensure product improvement
What are some Air Leak Testing methods?
Most of the time, users are not aware of the air leakage from their compressed air systems. By the time they detect the leakages, a lot of money and energy have already been lost. Although some leaks can just be found by listening, major ones are either inaudible or inaccessible.
The most common practices in the industry to identify air leakages are:
No load test for leak quantification
Leak Identification through an ultrasonic leak detector
The most widely used approach is the ultrasound leak detection method for faster detection and prevention of air leakages. Since a leak site creates a turbulent flow with ultrasound components, ultrasound detectors can identify leakages no matter how noisy the environment is.
Should you want to identify and fix inaccessible leaks in your unit, count on Rajdeep experts and solutions.
A quick fix solution for long term results
To prevent energy loss and ensure optimal performance of your air compressor system, Rajdeep brings you a complete compressed air leak check program, providing a leakage identification test with ultrasonic leak detector camera at the site without interrupting your production.
Our experience engineer will trace the complete compressed air line network to find out the leakage points, quantify the leaks in terms of volume
flow to understand the severity of leaks and list the leakages with photographs and leak tag. At the end of the Air Leak Check program, you will receive a detailed report of in-depth evaluation of problems along with recommendations for leak repair, and save up to 30% of energy immediately by closing the energy gap.
-> Quick
-> Cost Saving
-> Sustainable
-> Quick
-> Cost Saving
-> Sustainable
Do you want to fix air leakages and see what differences it makes to your air system? Schedule an appointment with our expert representative and save your time and money.